Formerly known as Admiral Overseas Corporation, AOC Technology was founded in Taiwan in 1967. Now it has grown into a global leader in LCD and TV intelligent manufacturing with 13 factories and an annual output of over 60 million units. AOC Technology has long maintained the its world’s first place in LCD production and sales volume, accounting for more than 35% of the total global LCD market, and ranking top five in LCD TV production and sales volume in the global LCD TV market.
More than a decade ago, AOC began to use SFIS solutions. With the expansion of the group, AOC Technology has been faced with new digital problems as follows:
1.The differences in factory management modes, product forms and customer requirements, resulting in difficulties in system management.
2.The functions of the original system have been increased, leading to lengthy and disorderly functional modules and blurred boundaries.
3.Lean management requirements need to be supported in the system.
4.It is necessary to comprehensively build equipment interconnection to lay a foundation of intelligent manufacturing.
Facing the situcation: labor cost higher, increasingly fierce competition and diversified customer requirements, AOC intends to put tin place a digital factory information system, so as to ensure its long-term development and build a world-class brand, improve the operating efficiency and reduce manufacturing costs. The digital factory information system is expected to meet the following requirements:
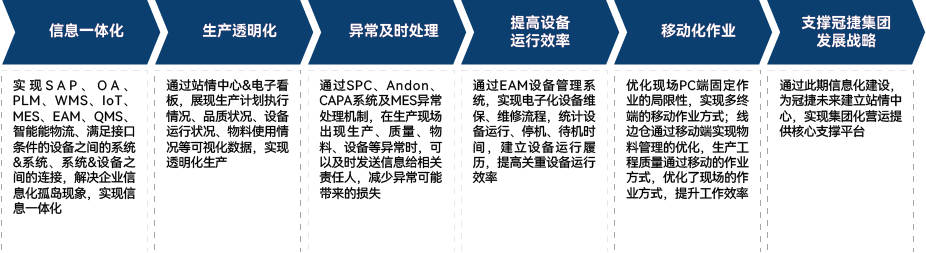
In combination of the efficient global collaboration strategy of AOC Technology, the IMS-MOM system helps establish a multi-factory and multi-organization scientific management system and position AOC Technology at the top of the global display industry:
1.Realize interconnection between systems and equipment such as SAP, OA, PLM, WMS, IoT, MES, EAM, QMS, intelligent logistics, equipment offering interfaces, solve the problem of isolated enterprise information and achieve information integration.
2.Through kanban and statements, visual data such as production plan implementation, quality status, equipment operation status and material use status are displayed to achieve transparent production.
3. Through SPC, Andon, CAPA system and MES anomaly processing mechanism, information can be promptly sent to the relevant responsible person, reduce the possible loss thereby caused by anomalies in case of production, quality, materials and equipment anomalies on the production site.
4.Establish electronic equipment maintenance process through the EAM system, count equipment operation, shutdown and standby time, establish equipment operation history, improve the operation efficiency of key and heavy equipment.
5.Optimize the limitations of PC fixed operation on site and realize the multi-terminal mobile operation mode; the material management of line warehouses is optimized through the mobile terminal, and the production engineering quality is optimized and work efficiency improved through the site mobile operation mode.
6.Through multi-stage information construction, a station center will be established for AOC in the future, so as to provide a core support platform for the establishment of group operation in the future.
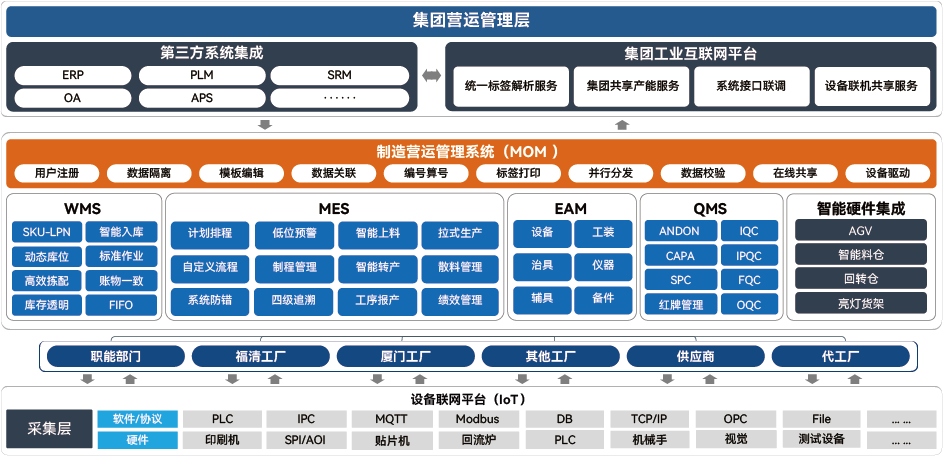
1. The group-wide MOM system is constructed to replace the original SFIS.
2. Realize the interconnection of existing systems and production core equipment, and lay the foundation of intelligent manufacturing information technology.
3. The system is imported to Fuqing Factory in Phase I, bringing about the following benefits:
At least 30 employees reduced directly
Equipment failure time and downtime reduced by 2%
Enhanced switchover efficiency turned into productivity: 29 SMT lines optimized by 166.3 million points/year