The Company is specialized in special railway signal equipment and track traffic signal control equipment integrating science and technology research and development, production and manufacturing, product sales, technical services, and a secondary wholly-owned subsidiary of CRSC Research & Design Institute Group Co.,Ltd. It’s a High-tech Enterprise and Patent Demonstration Enterprise of Beijing Municipality, and a National Civilized Unit. Built with international electronic assembly production lines, debugging and testing production line of train control system equipment and equipped with corresponding product experiment, testing and testing system equipment, the Company can produce all series of China Railway CTCS0-3 train control system equipment and provide on-site technical service of train control system equipment, winning the full recognition of customers and owners.
1. The existing ERP (SAP) system and PLM (Windchill) system can’t effectively guide the manufacturing operations, and the original barcode traceability software can’t meet the digital transformation and upgrading requirements of the enterprise, resulting in isolated information.
2. The traditional storage and production management mode can’t effectively trace and monitor the production operation of employees, which may easily lead to management loopholes and non-transparency.
3. The railway signal industry has high requirements for site control and traceability. There are still many manual recording operations in existing production and manufacturing and quality management, resulting in heavy quality inspection and audit workload, and no systematic 4M accurate traceability in the manufacturing process.
4. The irregular equipment running status has made it impossible to promptly identify the production bottlenecks and issues, and collect equipment production data.
5. The large number of paper work records leads to tedious document management.
1. Establish the equipment IoT platform to collect data of equipment status, process parameters and environmental parameters.
2. Based on the visual platform, the MES collects data such as plan execution status, process status, pass rate, efficiency and equipment operation status obtained in real time from each collection point, carries out comprehensive monitoring, management and analysis of production, and helps the production command department of the enterprise to monitor and manage the production site. promptly make corresponding adjustment and scheduling to build a material intelligent warehousing management module, subdivide the operation mode in the warehouse, standardize the warehouse operation process. The warehouse lean management level is improved through the use of barcode, automation equipment and other technologies to trace the whole process from the entry of raw materials to the warehouse to products delivery from the warehouse.
3. Through the integration with ERP, PLM and other information systems and equipment interfaces, the basic data, product information, production plan and production process data can be shared among multiple systems to ensure one time data entry and multi-platform sharing, and data synchronization and consistency. Further through the integration with the PLM and ERP systems, accurate design drawings, process documents, technical notices, software and related processing instructions or data can be promptly provided for the production lines. Production records, inspection records and handover records in the production process are managed electronically and systematically. A manufacturing specification management system is established in the MES to realize the information sharing of manufacturing specification, ensure the timely transmission of information, and guide the business operations of production executives in accordance with the specification.
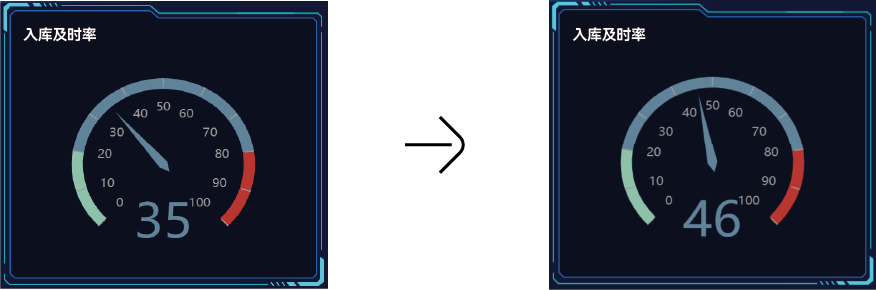
1. Average incoming inspection cycle reduced from 15 days to 9 days, resulting in an increase of timeliness rate from 35% to 46%.
2. Warehouse picking efficiency enhanced by 10%.
3. Scheduling system improved from advance material completion to system completion analysis + material preemption, reducing 1 employee and saving 60m2 of warehouse area.
4. With the help of production scheduling tools, the existing factory, workshop, team/group, section multi-level operation planning system is optimized to deliver production plans direct to the process and the team/group (or equipment). Immediate feedback on plan execution can be obtained and quick readjustment for exceptions can be made.
5. Realize seamless connection with ERP/PLM, collect the data of key production equipment, testing equipment and energy consumption, temperature and humidity environment of the production lines, and achieve comprehensive paperless operations.