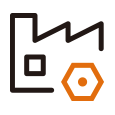
Complicated warehousing management because of extensive product structures
A wide variety of materials, complex models; lack of timeliness and accuracy of warehouse data; a lot of waste in the delivery and signing of a large number of paper documents.
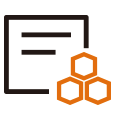
New challenges in production planning and management
Product structure diversification, non-transparent production process information; insufficient process traceability, no process fool-proofing and error-proof measures; insufficient accuracy and timeliness of process data collection.
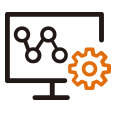
Increasingly difficult quality control and improvement
The complex and changeable production process results in increasingly more uncontrollable factors influencing production and product quality; insufficient quality data collection and analysis ability.
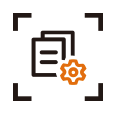
Increasingly high requirements for factory inspection of customers
With the gradual increase of finished vehicle customers, there is an increasingly high frequency of site audit. While vehicle factory gradually improve the requirements on raw materials, process control, quality management and other relevant aspects, traditional management methods can’t meet customer requirements.
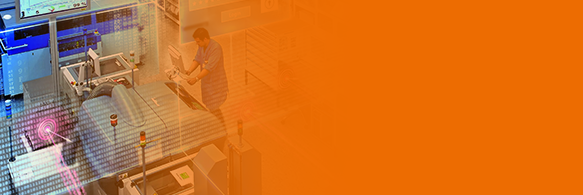
IoT(Internet of Terminals)
Realize “STS”, unblock the system data flow and information flow, seamlessly connect the systems, and form the closed-loop management of factory data; realize “MTM”, collect and analyze key equipment data and conduct formula management, and provide data support for capacity improvement and cost reduction.
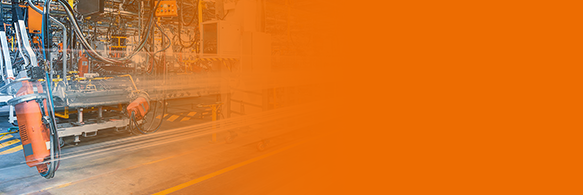
MES(Manufacturing Execution System)
The system realizes the monitoring, traceability and early warning of production factors and achieves material, workshop and production line management. All kinds of kanban promptly give feedback on production line data to establish a 4M traceability and 6M comprehensive error prevention system; the comprehensive visualized and digital operation management of production data is realized.
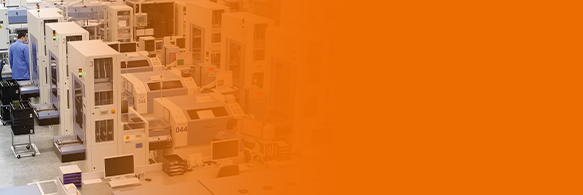
WMS(Warehouse Management System)
The warehousing and logistics and distribution management is optimized, the stock loaction mangement is realized,realize the real-time interaction with ERP, WMS, and MES data.The material distribution mode is comprehensively optimized, and the information transmission is electronic and timely.Improve the storage operation efficiency and optimize the on-site personnel orgnaization.
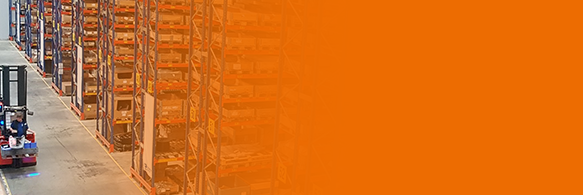
QMS(Quality Management System)
Realize whole-process control, monitor the quality problems of materials, semi-finished products and finished products, speed up the handling of quality anomaly events; keep records of production process information on materials, processes and personnel; establish two-way traceability between products and components.
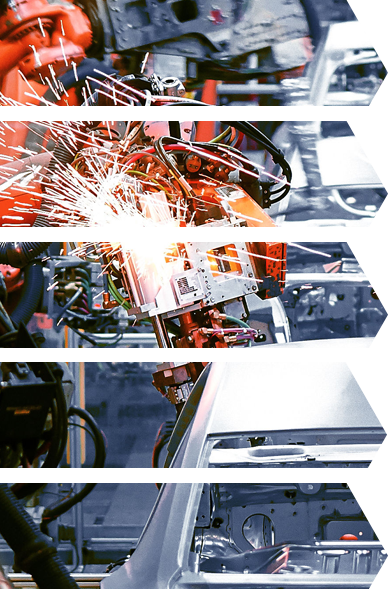
Improvement of lean material management
According to the SKU of different materials, the management of different granularity is developed, the material achieves 100% bar code fine management, the dynamic stock location management is realized, the storage put in-and- put out efficiency is improved by about 40%, and the storage, transportation and loading and unloading manpower are reduced by about 15%.
Improvement of production efficiency
Real-time control of the completion of the production plan can be realized through the production management system. During the production process, the WIP is decreased by about 65%, the capacity increased by about 18%, the production switchover speed increased by about 35%, and the planning period decreased by about 4%.
Improvement of quality control capabilities
Through the digital system, the 5M1E all-round control and system fool-proofing and error prevention management in the production process are realized. Meanwhile, the traditional paper document search and tracking is broken. Through the system, the forward and backward tracking can be quickly conducted, reducing the occurrence rate of process anomaly by about 42% and customer complaints by about 60%.
Seamless connection of information system and equipment
Fully realize STS and MTM, perfectly solve the problem of no execution control in ERP, greatly reduce personnel staffing; realize paperless operation, equipment connection, real-time acquisition of equipment operation data, real-time monitoring of KPI data, time rate, performance rate, pass rate, OEE, and quality data.
Improvement the pass rate of vehicle factory
Comprehensively improve the control ability and management level of materials, production and quality by building a digital intelligent manufacturing factory, and thus improve the customer audit pass rate to 100%, reduce the serious nonconformities of the audit by about 98%, and general and minor nonconformities by about 65%.
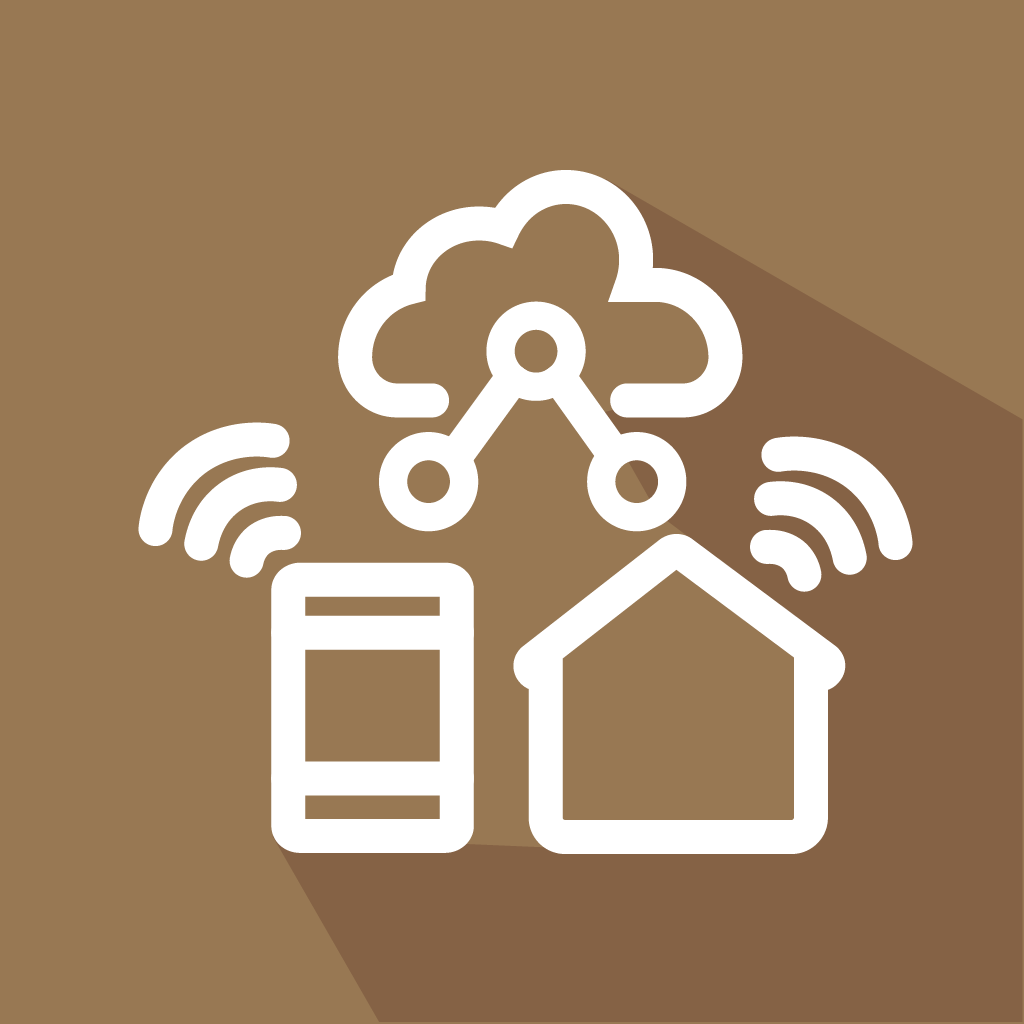
IoT
Internet of Terminals
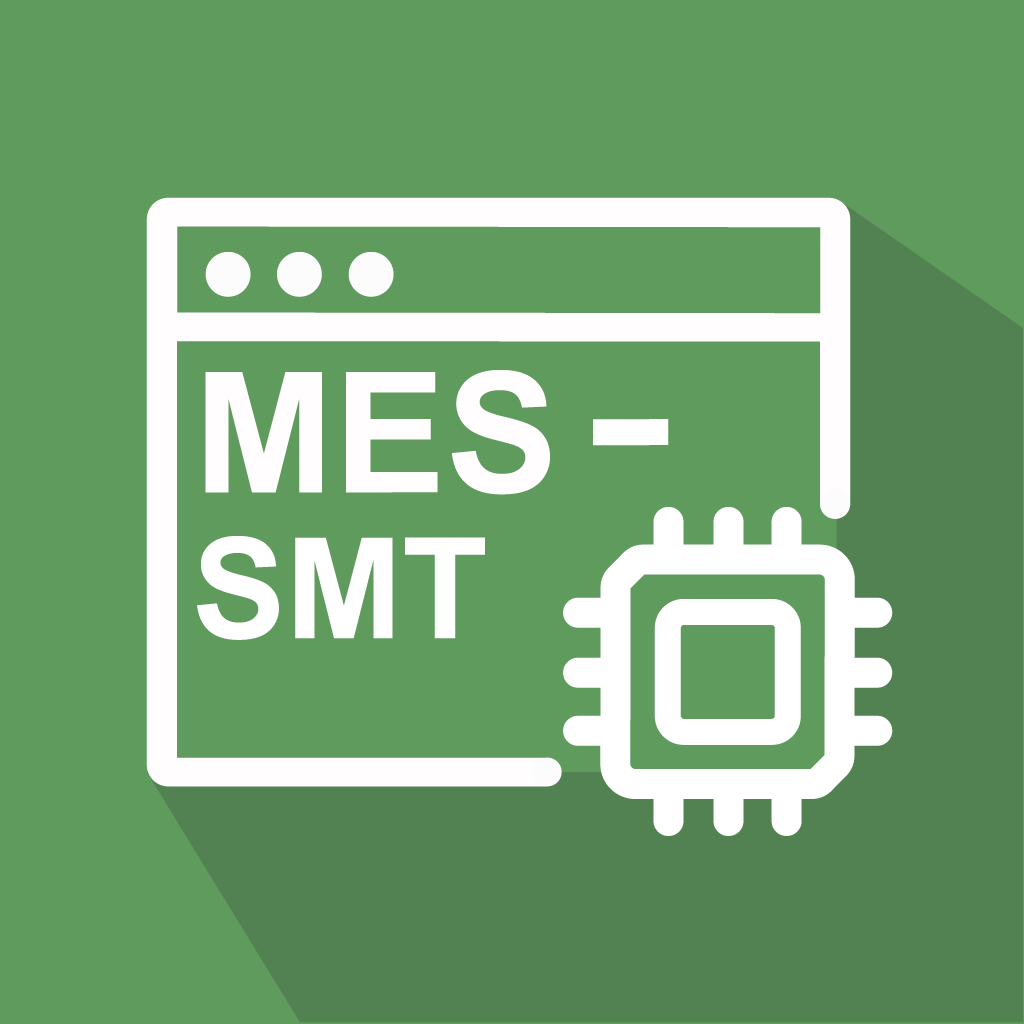
MES
Manufacturing Execution System
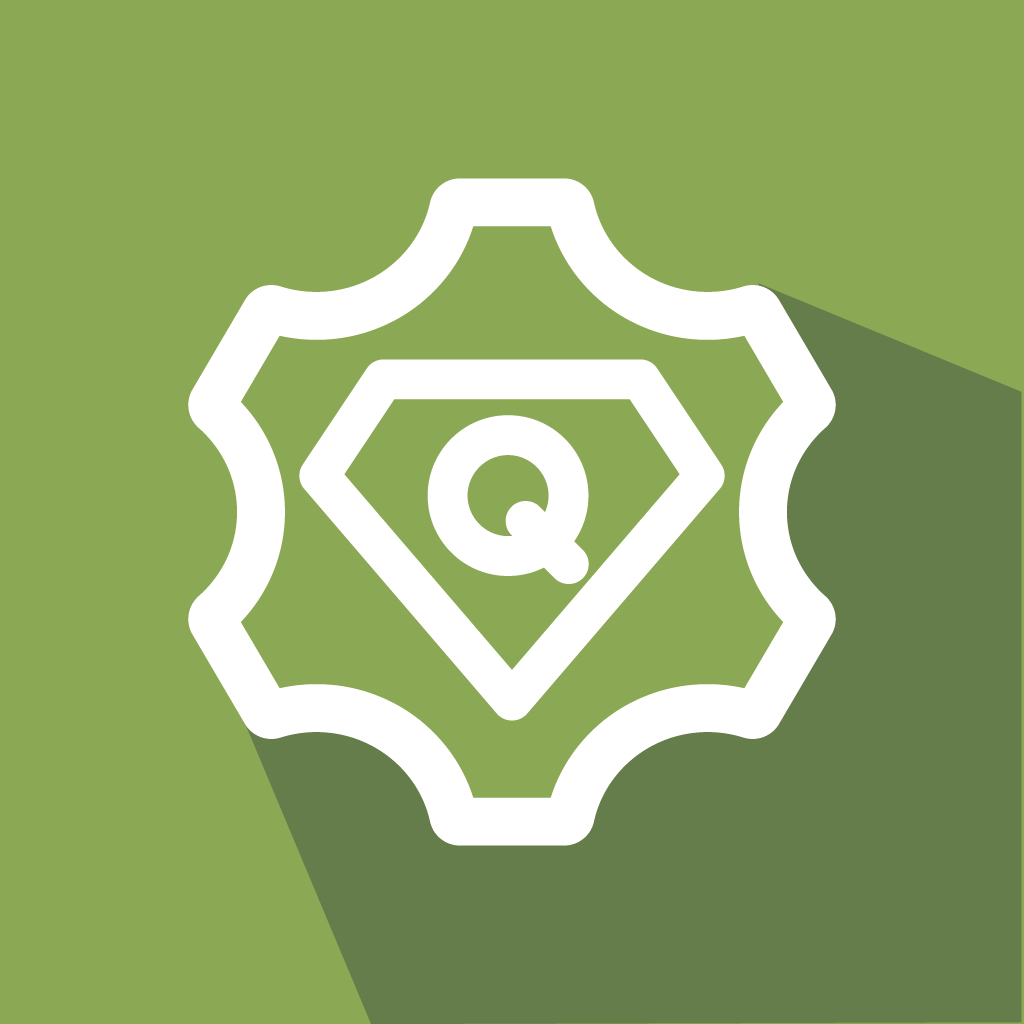
QMS
Quality Management System
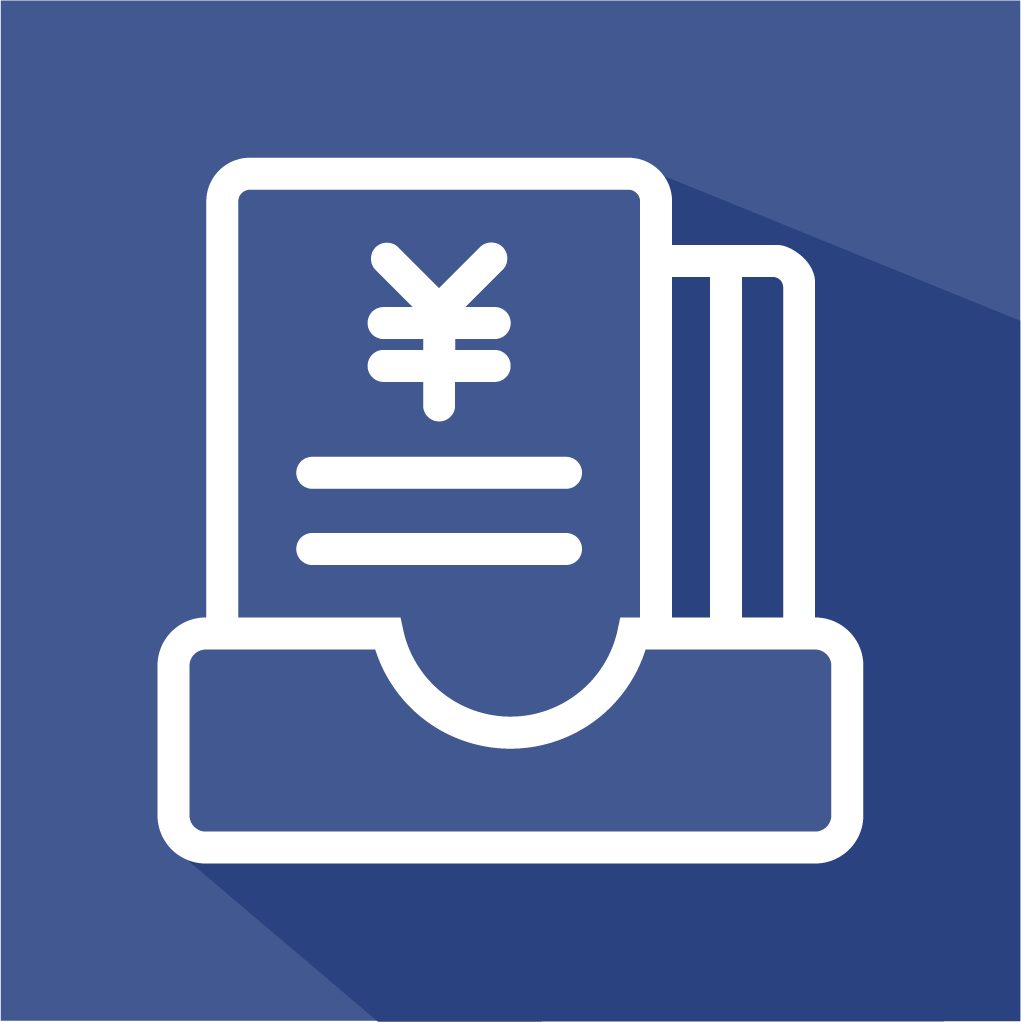
EAM
Enterprise Asset Management System

Shenzhen DJI Zhuojian Technology Co., LTD
Shenzhen, Guangdong
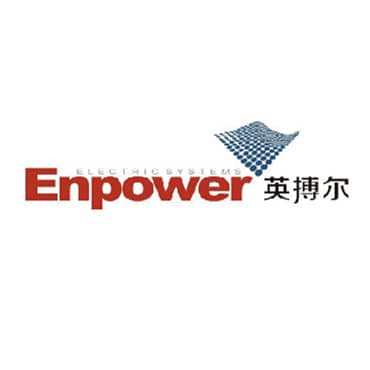
Enpower Electric Co., LTD
Zhuhai,Guangdong
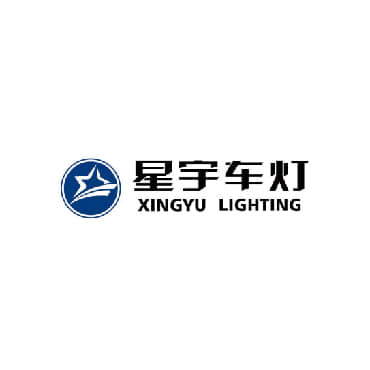
Changchou Xingyu Lightning Co., LTD
Changzhou, Jiangsu